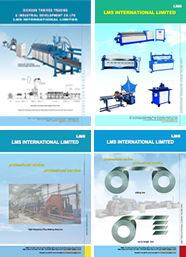
Product Detail
Product Information
Door frame roll forming with off-line hole-punching
MODEL: 220 X 72.8 X 1.2 – 2.0 MM
DRAWING & INSTALLATION OF DOOR FRAME
DOOR FRAME FORMING STEP:
1.MAIN FRAME:
Material Coil – Decoiling – Roll-Forming – Hydraulic Cutting-Off – Roll-Formed Main Frame Profile – PLC Controlling
2.LEFT HINGE ON MAIN FRAME:
Roll-Formed Main Frame Profile – Punching by Hydraulic Punch with 3-Working-Position – Left Main Frame Profile with 3 Hinges on
3.RIGHT KEY-HOLE ON MAIN FRAME:
Roll-Formed Main Frame Profile – Punching by Hydraulic Punch – Right Main Frame Profile with Key-Hole on
4.45°BEVEL CUTTING:
Roll-Formed & Punched Main Frame Profile – Bevel Cutting by Sawing Cutter – Finished Main Frame Profile
5.ASSEMBLING:
Top Frame, Bottom Frame, Left Frame & Right Frame Profile with 45°Bevel Cutting – Welding Together
TECHNICAL PARAMETER
MAIN FRAME roll forming machine 1 FULL SET
A.MATERIAL AND PROFILE SPECIFICATION:
1.Materials:Q195, HCR Steel Coil
2.Material Thickness:1.2 – 2.0 mm
3.Profile Width:220.0 mm
4.Profile Height:72.8 mm
5.Profile Specification:220.0 x 72.8 x 1.2 – 2.0 mm, same as drawing
B.PRODUCTION PROCESS:
material coil – decoiling – roll forming – hydraulic cutting-off – main frame profile – PLC controlling
C.COMPONENTS
1.DECOILER:1 SET
(1)Operational Type:Manual Expansion
(2)Max. Width:400 mm
(3)Inner Diameter:Φ400 – Φ450 mm
(4)Out Diameter:1700 mm
(5)Max. Loading Capacity:2000 kgs
2.ROLL FORMING MACHINE:1 SET
(1)Rollers Stations:20 Nos, 5 Nos for Straighten Rollers
(2)Rollers' Material:GCr15 steel
(3)Rollers' Hardness after Heat Treatment:HRC55 – 57
(4)Main Shaft Diameter:50 mm
(5)Main Shaft Material:45# Steel
(6)Machine Frame Steel Thickness:25 mm
(7)Gears' Material:45# Steel, after High Frequency Treatment
(8)Gears'Thickness:45 mm
(9)Main Bearing:60308
(10)Motor Power:15 kw
(11)Speed Reducer Model:QZ 400
(12)Rolling Speed:2 – 10 m / min; Adjustable
(13)Equipped Device: Water Cooler Device
3.CUT-OFF DEVICE:1 SET
(1)Cut-Off Type:Hydraulic, Automatic Cut-Off
(2)Cut-Off Modular:1 Set, Selvage Cutting-Off
(3)Material for Cut-Off Modular:GCr12 MOV Steel
(4)Hardness for Heat Treatment:HRC57 – 61
(5)Motor Power:3 kw
4.RUN-OUT TABLE:1 SET
(1)Type:Pneumatic Run-Out Table
(2)Driven:Controlled by Pneumatic Cylinder
(3)Table Structure:Welded by 8# Channel Steel
(4)Table Length:6 Meters
5.ELECTRONIC CONTROL SYSTEM
(1)PLC:Mitsubishi, Japan
(2)Controller:Touchable Screen
(3)Speed Adjuster:Frequency Converter, Japan
(4)Main Electronic Components:Schneider & Silin, Taiwan
(5)Electric Control Panel:Full-Sealed, Ventilation Cooler
(6)Control System Power:Overload Protection
(7)Electric Control Cabinet:By Aviation Connection Plugs
(8)Cut-Off Step:Machine Stopped, then Cut-Off
(9)Profile Length Control:Encoder, Tolerance within ± 1 mm
(10)Power Supplier:380V, 50Hz, 3Phs.
HINGE HOLE-PUNCHING MACHINE 1 SET FOR HINGE FORMING
1.A set of 3 working position hole-punching machines is equipped, adopted 3 hydraulic presses, width adjustable.
2.Hinge hole-punching machine is composed by the hydraulic press support, 3 sets of hydraulic press, 3 sets of hinge hole-punching modular, machine support, etc. The middle one is fixed while the others on both sides are changeable by screw, up to the required length of door frame. On hole-punching, 3 sets of hydraulic presses work simultaneously, to punch out 3 hinge hole.
3.Max. center distance between both sides of hydraulic press is 2000 mm.
4.1 hydraulic pump stands is equipped, controlling 4 cylinders, which function with keyhole hydraulic punch.
5.Motor for hydraulic stand is 4 kw, sheared with keyhole hydraulic punch.
HYDRAULIC PUNCH 1 SET FOR KEYHOLE PUNCHING
1.Hydraulic punch is equipped for keyhole punching, which size is illustrated in the above drawing.
2.1 set of hole-punching modular is equipped.
3.1 hydraulic pump stands is equipped, controlling 4 cylinders, which function with hinges hydraulic punch.
4.Motor for hydraulic stand is 4 kw, sheared with hinges hydraulic punch.
SAWING CUTTER 1 SET (OPTIONAL) FOR 45°BEVEL CUTTING
1.1 set of standard model sawing machine is equipped for main frame 45°bevel cutting.
2.2 sets of clamping modular are combined-used with sawing machine, left and right 45°bevel cutting.
DELIVERY DAYS
80 DAYS
INSTALLATION, MAINTENANCE AND OPERATOR TRAINING
1 year guarantee for spare parts is included in quotation.
The operator training in our factory is free.
The technician could be sent for installation and operator training at site, but the fee should be discussed separately.
![]() |
![]() |
![]() |
![]() |
![]() |
![]() |
Related Product